Automotive Injection Molding: Revolutionizing the Industry
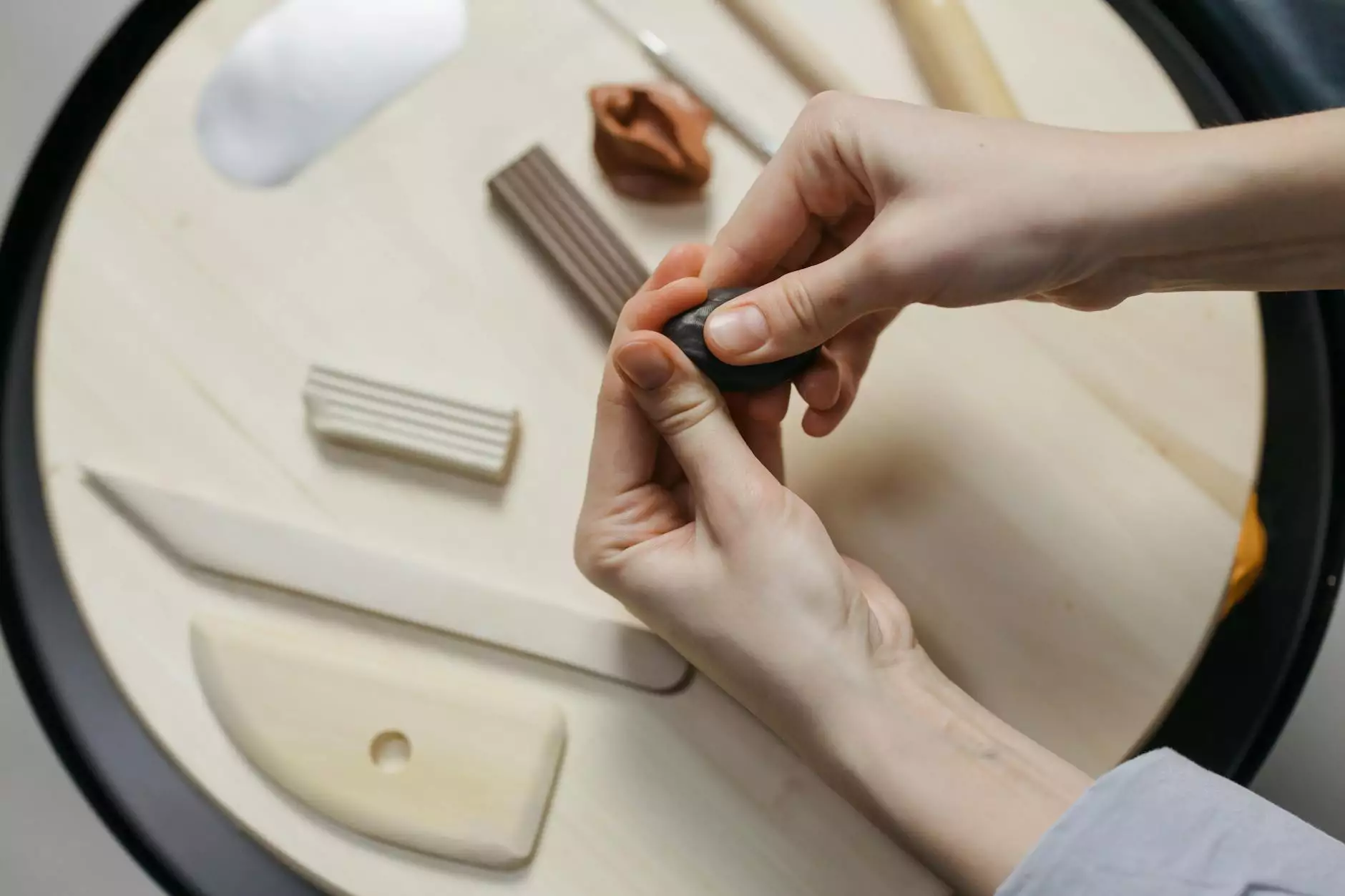
Automotive injection molding stands at the forefront of manufacturing technology, particularly in the automotive sector. This sophisticated process not only shapes components with precision but also plays a vital role in enhancing the performance and economics of vehicle production. In this comprehensive guide, we will delve deep into the intricacies of automotive injection molding, its benefits, applications, and why it is essential for modern manufacturers.
Understanding Automotive Injection Molding
At its core, automotive injection molding is a manufacturing technique that involves injecting molten material into a mold to create various components. This process is predominantly used for plastic parts in vehicles, which can range from small clips to significant structural elements. The ability to create complex geometries with high precision is what makes this technique invaluable.
The Process Explained
The injection molding process comprises several key steps:
- Material Selection: The first step involves selecting the appropriate thermoplastic material. Common choices include ABS, polypropylene, and polycarbonate, each offering distinct properties suited to different automotive applications.
- Mold Design: A well-designed mold is critical for achieving the desired component shape and quality. CAD software is frequently used to design molds that maximize efficiency and reduce production times.
- Injection: Once the mold is ready, the selected material is heated until molten and then injected into the mold under high pressure. This ensures that the material fills every cavity and detail of the mold.
- Cooling: After injection, the material begins to cool and solidify. The cooling rate must be carefully controlled to avoid defects like warping or shrinking.
- Mold Opening: Once cooled, the mold is opened, and the newly formed part is ejected. This stage requires precision to prevent damage to the part or the mold.
- Finishing: Finally, any required finishing touches, such as trimming or surface treatments, are applied to ensure the part meets specifications.
Benefits of Automotive Injection Molding
Automotive injection molding offers numerous advantages, making it the preferred choice among manufacturers:
- Cost Efficiency: The initial investment in molds can be high, but the ability to produce large quantities of identical parts quickly greatly reduces the cost per unit.
- High Precision: Advanced machinery enables the production of components with tight tolerances, crucial for ensuring safety and performance in automotive applications.
- Material Versatility: Various materials can be used depending on the performance requirements, allowing for a broad range of applications in multiple vehicle types.
- Minimal Waste: Injection molding produces minimal scrap material, as the process is highly efficient in material usage.
- Complex Shapes: The flexibility in mold design allows for the creation of intricate shapes and features that may be impossible with traditional manufacturing processes.
Applications of Automotive Injection Molding
With its powerful capabilities, automotive injection molding is utilized in various components and systems within vehicles:
Interior Components
Injection molding is extensively used to produce interior parts such as:
- Dashboard Components: Molded dashboard panels with varying textures and finishes enhance aesthetics and functionality.
- Door Panels: These are critical not only for aesthetics but for sound insulation and impact resistance.
- Console and Cup Holders: Customizable designs allow for ergonomic usability and efficient space management.
Exterior Parts
Exterior applications include:
- Bumpers: Lightweight and impact-resistant bumpers are crucial for vehicle safety and efficiency.
- Grilles: Intricate designs can be manufactured to enhance airflow and vehicle aesthetics.
- Body Panels: These parts benefit from the strength and lightweight properties of molded plastics.
Functional Components
Additionally, injection molding is key in producing functional automotive components such as:
- Clip and Fasteners: Essential for assembly, molded clips provide reliability and ease of replacement.
- Housings for Electronics: Protecting sensitive electronic components is vital, and molded housings provide durability.
- Cooling Fans: Efficient cooling mechanisms rely on durable, precisely molded fan components.
Innovations in Automotive Injection Molding Technology
The automotive industry is continually evolving, with advancements in injection molding technology providing enhanced capabilities:
3D Printing for Mold Making
Innovations in 3D printing technology allow for rapid prototyping of injection molds, significantly reducing lead times and costs. This facilitates faster product development and testing in the automotive sector.
Hybrid Molding Techniques
Hybrid techniques that combine injection molding with other manufacturing methods, such as injection stretch blow molding, are on the rise. These techniques provide unique properties and improved performance for automotive components.
Recyclable Materials
The push towards sustainability in automotive manufacturing has led to greater use of recyclable materials in injection molding processes. This not only reduces the environmental impact but also aligns with global trends toward eco-friendly production.
Challenges in the Automotive Injection Molding Industry
Despite its benefits, the automotive injection molding industry faces several challenges:
High Initial Costs
While cost-efficient in mass production, the initial investment in molds and machinery can be prohibitive for smaller manufacturers.
Material Limitations
Not all materials are suitable for injection molding. Manufacturers must carefully choose materials that align with their performance requirements.
Complexity of Design Changes
Once a mold is created, making design changes can be costly and time-consuming, resulting in potential delays in production.
The Future of Automotive Injection Molding
The future of automotive injection molding looks promising, with continuous research and development driving innovations. Technologies such as:
- Smart Manufacturing: Integration of IoT in manufacturing processes to enhance efficiency and reduce downtime.
- Advanced Materials: Continuous development of stronger, lighter materials that can further enhance vehicle performance and fuel efficiency.
- Automation: Increased use of robotics in injection molding processes to improve precision and reduce labor costs.
The Role of Metal Fabricators in Automotive Injection Molding
Metal fabricators play a crucial role in the automotive injection molding ecosystem. They provide the molds that make the injection molding process possible, ensuring they are designed for optimal performance and longevity. Manufacturers like DeepMould.net specialize in creating high-quality molds that cater to the specific needs of automotive clients, contributing to the overall success of the injection molding process.
From prototype development to production mold manufacturing, collaboration between metal fabricators and automotive manufacturers results in superior products that drive the industry forward.
Conclusion
Automotive injection molding is a game-changing process that has transformed how vehicles are produced. With its ability to create high-precision, complex shapes at a lower cost, it is a vital component of modern automotive manufacturing. As technology progresses and the industry evolves, we can expect to see even more remarkable advancements in this field.
For manufacturers looking to stay ahead in the competitive automotive market, embracing the innovations in automotive injection molding and collaborating with expert metal fabricators like DeepMould.net will be essential for success.